NEWS
TEL:+86 510 83571868
FAX:+86 510 83571878
Email:wxanlida888@126. com
FAX:+86 510 83571878
Email:wxanlida888@126. com
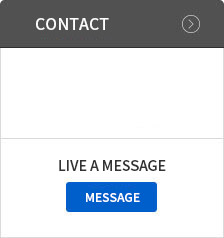
Application and Structure of Three-phase Asynchronous Motor
Update time:2019-04-01 19:41:00Clicks:1308
Motor is the power equipment that converts electric energy into mechanical energy and outputs mechanical torque. Motors are widely used in modern machinery.
General motors can be divided into DC motor and AC motor. AC motor can be divided into single-pha
I. Overview of Motors
Motor is the power equipment that converts electric energy into mechanical energy and outputs mechanical torque. Motors are widely used in modern machinery.
General motors can be divided into DC motor and AC motor. AC motor can be divided into single-phase motor and three-phase motor according to the number of power supply phases. Three-phase motor can be divided into synchronous motor and asynchronous motor. Asynchronous motor can be divided into cage motor and winding motor according to different rotor structures.
Three-phase asynchronous motor has the advantages of simple structure, convenient maintenance and reliable operation. Compared with other motors with the same capacity, it has the advantages of light weight, low cost and low price. Therefore, it is widely used to drive medium and small rolling mills, various machine tools, light industrial machinery and blowers. According to statistics, about 90% of electric traction machines in China use asynchronous motors, of which small asynchronous motors account for more than 70%. Asynchronous motors account for more than 60% of the total load of the power grid.
2. Basic structure of three-phase asynchronous motor
Three-phase cage asynchronous motor is mainly composed of stator and rotor, as shown in Figure 4-10.
The stator part of a three-phase asynchronous motor includes a base, a stator core and a stator winding. The frame is made of cast iron or cast steel. It supports the stator core. Stator cores are made of insulated silicon steel sheets, with grooved holes in the inner circle and stator windings embedded in the grooves, as shown in Fig. 4-11.
The stator winding is the circuit part of the stator, which consists of three-phase symmetrical windings. Each phase of the three-phase winding is independent of each other. It is embedded in the stator slot according to the electric angle of 120 difference, and insulated with the stator core. The first end of stator winding is represented by U1, V1 and W1 respectively, while the end of stator winding is represented by U2, V2 and W2 respectively.
The rotor consists of rotor core, rotor winding and rotating shaft. The rotor core is made of silicon steel sheets with grooves in the outer circle, and copper bars (or cast aluminium) are placed in the grooves. The two ends of the core are connected by conductive end rings to form a short circuit. If the core of the rotor is removed, the structure of the rotor is similar to that of the cage, as shown in Figure 4-12.
Winding asynchronous motor has only different rotor structure. Its rotor is composed of windings, which are also three-phase like stator windings.
Rotation Principle of Three-phase Asynchronous Motor
In order to explain how the rotor of three-phase asynchronous motor rotates, two demonstration experiments are done first.
As shown in Fig. 4-13, there is a horseshoe magnet with a handle. A conductive squirrel cage rotor can rotate freely in the middle of the magnetic pole. There is no mechanical connection between the rotor and the magnetic pole. When the handle is shaken to rotate the horseshoe magnet, the squirrel cage rotor can be seen to rotate with the magnet. The faster the handle rocks, the faster the rotor rotates. If the rotation direction of the magnet is changed, the rotation direction of the squirrel cage rotor also changes.
From the above experiments, it can be seen that the first condition of rotor rotation is to have a rotating magnetic field.
2. Generation of Rotating Magnetic Field of Stator
In the actual cage asynchronous motor, the rotating magnetic field is generated by three-phase alternating current in the stator winding.
If the stator core of three-phase asynchronous motor has three relative symmetrical windings U1-U2, V1-V2, W1-W2, and is connected in star shape (Y), when connected with three-phase symmetrical power supply, current in three-phase symmetrical winding passes through, that is:
The waveform of three-phase symmetrical current is shown in Fig. 4-14. It is stipulated that the current flows from the end of the winding and from the end of the winding in the positive half cycle, while the current flows from the end of the winding and from the end of the winding in the negative half cycle. When AC current passes through three-phase windings, each phase winding will produce a sinusoidal magnetic field, and the composite magnetic field of three-phase windings will continuously change its direction over time to form a rotating magnetic field, as shown in Fig. 4-15.
Formula (4-3) shows that the rotational speed of the rotating magnetic field decreases with the increase of the number of magnetic poles. Table 4-2 shows the rotating magnetic field speed corresponding to the logarithm of magnetic poles at the power supply frequency of 50 Hz.
Table 4-2 Relation between Pole Logarithm and Rotating Magnetic Field Speed at 50 Hz Power Supply Frequency
Logarithm of magnetic poles
One
Two
Three
Four
Five
Six
Rotating magnetic field speed (r/min)
3000
1500
1000
Seven hundred and fifty
Six hundred
Five hundred
3. Rotating magnetic field's effect on rotor
The rotating magnetic field generated in the stator will cut the copper bar of the rotor. At this time, the magnetic field can be regarded as immovable and the rotor moves relative to the magnetic field. Assuming that the rotating magnetic field rotates clockwise, the rotor can be regarded as rotating counterclockwise relative to the magnetic field, as shown in Fig. 4-17. Induced electromotive force and induced current are generated in the copper bar of the rotor, and their direction can be determined by the right-hand rule. In the upper half of the rotor, the direction of the induced current points to the reader, while in the lower half of the rotor, the direction of the induced current deviates from the reader.
The copper bars loaded with induced current in the rotor interact with the rotating magnetic field to produce electromagnetic force. According to the left hand rule, the force on the top copper bar of the rotor is to the right, and the force on the bottom copper bar is to the left. These two forces are equal in magnitude and opposite in direction, forming electromagnetic torque, so the rotor rotates with the rotating magnetic field, which is the rotating principle of three-phase cage asynchronous motor. Rotor speed must be less than synchronous speed. If there is no relative motion between the rotor and the rotating magnetic field, the cadmium bar on the rotor can not cut the magnetic induction line, and the induction electromotive force and induction current will not be generated, and the electromagnetic torque will not be formed, so the rotor can not run at the synchronous speed. In fact, the rotor speed is always less than the synchronous speed, that is. That is to say, rotor speed
Motor is the power equipment that converts electric energy into mechanical energy and outputs mechanical torque. Motors are widely used in modern machinery.
General motors can be divided into DC motor and AC motor. AC motor can be divided into single-phase motor and three-phase motor according to the number of power supply phases. Three-phase motor can be divided into synchronous motor and asynchronous motor. Asynchronous motor can be divided into cage motor and winding motor according to different rotor structures.
Three-phase asynchronous motor has the advantages of simple structure, convenient maintenance and reliable operation. Compared with other motors with the same capacity, it has the advantages of light weight, low cost and low price. Therefore, it is widely used to drive medium and small rolling mills, various machine tools, light industrial machinery and blowers. According to statistics, about 90% of electric traction machines in China use asynchronous motors, of which small asynchronous motors account for more than 70%. Asynchronous motors account for more than 60% of the total load of the power grid.
2. Basic structure of three-phase asynchronous motor
Three-phase cage asynchronous motor is mainly composed of stator and rotor, as shown in Figure 4-10.
The stator part of a three-phase asynchronous motor includes a base, a stator core and a stator winding. The frame is made of cast iron or cast steel. It supports the stator core. Stator cores are made of insulated silicon steel sheets, with grooved holes in the inner circle and stator windings embedded in the grooves, as shown in Fig. 4-11.
The stator winding is the circuit part of the stator, which consists of three-phase symmetrical windings. Each phase of the three-phase winding is independent of each other. It is embedded in the stator slot according to the electric angle of 120 difference, and insulated with the stator core. The first end of stator winding is represented by U1, V1 and W1 respectively, while the end of stator winding is represented by U2, V2 and W2 respectively.
The rotor consists of rotor core, rotor winding and rotating shaft. The rotor core is made of silicon steel sheets with grooves in the outer circle, and copper bars (or cast aluminium) are placed in the grooves. The two ends of the core are connected by conductive end rings to form a short circuit. If the core of the rotor is removed, the structure of the rotor is similar to that of the cage, as shown in Figure 4-12.
Winding asynchronous motor has only different rotor structure. Its rotor is composed of windings, which are also three-phase like stator windings.
Rotation Principle of Three-phase Asynchronous Motor
In order to explain how the rotor of three-phase asynchronous motor rotates, two demonstration experiments are done first.
As shown in Fig. 4-13, there is a horseshoe magnet with a handle. A conductive squirrel cage rotor can rotate freely in the middle of the magnetic pole. There is no mechanical connection between the rotor and the magnetic pole. When the handle is shaken to rotate the horseshoe magnet, the squirrel cage rotor can be seen to rotate with the magnet. The faster the handle rocks, the faster the rotor rotates. If the rotation direction of the magnet is changed, the rotation direction of the squirrel cage rotor also changes.
From the above experiments, it can be seen that the first condition of rotor rotation is to have a rotating magnetic field.
2. Generation of Rotating Magnetic Field of Stator
In the actual cage asynchronous motor, the rotating magnetic field is generated by three-phase alternating current in the stator winding.
If the stator core of three-phase asynchronous motor has three relative symmetrical windings U1-U2, V1-V2, W1-W2, and is connected in star shape (Y), when connected with three-phase symmetrical power supply, current in three-phase symmetrical winding passes through, that is:
The waveform of three-phase symmetrical current is shown in Fig. 4-14. It is stipulated that the current flows from the end of the winding and from the end of the winding in the positive half cycle, while the current flows from the end of the winding and from the end of the winding in the negative half cycle. When AC current passes through three-phase windings, each phase winding will produce a sinusoidal magnetic field, and the composite magnetic field of three-phase windings will continuously change its direction over time to form a rotating magnetic field, as shown in Fig. 4-15.
Formula (4-3) shows that the rotational speed of the rotating magnetic field decreases with the increase of the number of magnetic poles. Table 4-2 shows the rotating magnetic field speed corresponding to the logarithm of magnetic poles at the power supply frequency of 50 Hz.
Table 4-2 Relation between Pole Logarithm and Rotating Magnetic Field Speed at 50 Hz Power Supply Frequency
Logarithm of magnetic poles
One
Two
Three
Four
Five
Six
Rotating magnetic field speed (r/min)
3000
1500
1000
Seven hundred and fifty
Six hundred
Five hundred
3. Rotating magnetic field's effect on rotor
The rotating magnetic field generated in the stator will cut the copper bar of the rotor. At this time, the magnetic field can be regarded as immovable and the rotor moves relative to the magnetic field. Assuming that the rotating magnetic field rotates clockwise, the rotor can be regarded as rotating counterclockwise relative to the magnetic field, as shown in Fig. 4-17. Induced electromotive force and induced current are generated in the copper bar of the rotor, and their direction can be determined by the right-hand rule. In the upper half of the rotor, the direction of the induced current points to the reader, while in the lower half of the rotor, the direction of the induced current deviates from the reader.
The copper bars loaded with induced current in the rotor interact with the rotating magnetic field to produce electromagnetic force. According to the left hand rule, the force on the top copper bar of the rotor is to the right, and the force on the bottom copper bar is to the left. These two forces are equal in magnitude and opposite in direction, forming electromagnetic torque, so the rotor rotates with the rotating magnetic field, which is the rotating principle of three-phase cage asynchronous motor. Rotor speed must be less than synchronous speed. If there is no relative motion between the rotor and the rotating magnetic field, the cadmium bar on the rotor can not cut the magnetic induction line, and the induction electromotive force and induction current will not be generated, and the electromagnetic torque will not be formed, so the rotor can not run at the synchronous speed. In fact, the rotor speed is always less than the synchronous speed, that is. That is to say, rotor speed